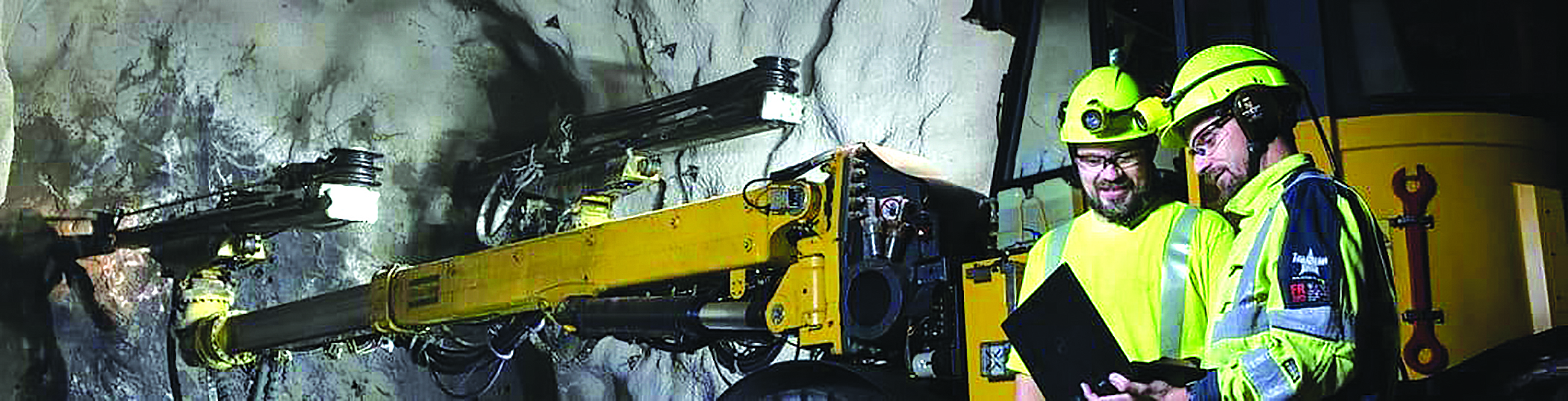
Safety and location monitoring of underground workers at Lundin Mining’s Zinkgruvan mine in Sweden will benefit from implementation of Mobilaris’ Virtual Tag positioning app, which runs on the mine’s LTE and Wi-Fi networks.
Digital technologies continue to make significant inroads into almost every facet of mining, offering the prospect of better mine site communications, improved asset tracking and equipment control capabilities, and faster, more-accurate data collection and analysis. A recent flurry of announcements from cellular communications providers such as Ericsson and Nokia, asset-location specialist Mobilaris and mine operators Boliden and Lundin highlight the quickening pace of technological progress and industry acceptance, particularly in the area of workforce location, tracking and notification functions.
In early June, Ericsson launched its private 5G platform, noting it offers secure and simple 4G LTE and 5G Standalone (SA) connectivity, primarily targeting the mining and process industries as well as ports and other industrial sectors. According to the company, it can be easily installed within hours at any facility and can be scaled to support larger coverage areas, more devices and higher capacity when needed. The product is designed to be flexible and will support a range of deployment sizes, depending on requirements, to suit varied needs. Businesses can manage their networks and integrate with IT/OT systems via an open API.
Ericsson said private 5G builds upon its 4G/5G radio and dual-mode core technology, enabling a wide variety of use cases for both indoor and outdoor environments while integrating well with business operations, devices and applications.
Obvious use cases include tracking assets and real-time automation, along with efficient quality inspections that can be performed via augmented reality or smart surveillance drones to increase worker safety, particularly in potentially hazardous environments such as mines. Ericsson quoted Peter Burman, program manager, mine automation, at Swedish mining company Boliden: “Automation, and safety through automation in our mining operations is an absolute must for us. Ericsson private 5G is exactly what Boliden needs to bring high quality, fast and secure connectivity into potentially hazardous environments allowing us to mobilize efficiency and safety improving use cases.”
Ericsson has been working with Mobilaris and other technology companies to develop both physical and app-based tagging solutions that will work with its 5G platform. For example, Mobilaris in May introduced the Companion, a durable cellular IoT device that provides secure asset tracking. The multipurpose tag collects information and positioning data using IoT technologies such as 5G and ultra-wideband (UWB).
According to Mobilaris and Ericsson, the 5G-ready device offers proximity triggers and collision alerts using sensors, monitoring, and real-time positioning of people, vehicles and moving assets. It can automatically react to hazardous gas emissions, humidity levels, barometric pressure and temperature. The information is shared in real time, enabling the wearer to react quickly. The device, said Mobilaris, is currently available and certified for use in Europe, North America and Australia.
Mobilaris also has been collaborating with Zinkgruvan Mining AB, part of Lundin Mining Corp., to set up a unique, full-site communication and positioning infrastructure at the Zinkgruvan mine.
The mine is located in south-central Sweden and has been in continuous operation since 1857, producing zinc, lead and copper concentrates. In 2019, Zinkgruvan Mining and Mobilaris started a digitalization project aimed at establishing a site-wide LTE network providing high speed and capacity, with seamless functionality between various areas across the site. As part of the project effort, Mobilaris, in cooperation with design house Sigma Connectivity, developed its Virtual Tag positioning app, which works with the mine’s new LTE network and Wi-Fi and answers a need to find a solution that didn’t require workers to carry additional equipment or devices.
The Virtual Tag, according to Mobilaris, is a mobile app that runs in the background on a worker’s Android smartphone. It enables seamless positioning when moving between underground, surface and indoors. The application continuously scans and reports radio references such as LTE radio cells, Wi-Fi access points, GPS and Bluetooth anchors. These references calculate the position in real-time via the Mobilaris Mining Intelligence platform, said Marcus Ek, product manager at Mobilaris.
In addition to enabling a flexible roll-out of positioning infrastructure, Virtual Tag combined with Bluetooth Low Energy (BLE) devices enables Zinkgruvan to decide in which areas better positioning accuracy can be provided. Håkan Mann, IT project manager at Zinkgruvan Mining, said, “For detailed positioning, we are using BLE beacons to send signals to our smart phones or tablets. Each BLE beacon has a unique ID which makes it possible to connect each beacon to a position in the mine map. For the deployment in the mine and inside buildings, we are going to use or place BLE beacons in zones and on assets where we need high precision positioning information.”
Craig Griffiths, mine manager, said the new digital infrastructure, using Mobilaris Situational Awareness, allows the position of vehicles, equipment, and personnel to be presented in a 3D user interface on the operations center monitoring screens, providing better control of operations and resources, while enabling workers to react to real-time situations.
In another initiative to improve safety at the Zinkgruvan site, Mobilaris’ Emergency Support application will be used to notify underground miners of an emergency via their Virtual Tags. The control room will be notified when users have received and acknowledged the alert, and rescue teams will be able to determine the location of miners underground to focus on those who have not yet evacuated or reached a refuge point.
Meanwhile, cellular communications provider Nokia announced in April it is partnering with telecom company Claro Chile to equip the new Gold Fields Salares Norte mine with a high-performance private wireless network. Being deployed is a private LTE/4.9G solution, including AirScale radio, small cells, packet core, IP routers and NetAct network management system. In total, the network will connect 150 sensors for operational processes, monitoring and accident prevention in addition to 72 connected vehicles and machines. Nokia and Claro will also provide professional services such as network design, testing and deployment. With this infrastructure, the network will enable critical voice, data, internet and video communications to improve employee safety, as well as operational efficiency and productivity.
Nokia, which claims more than 40 mines are now using its private LTE/4.9G and 5G networks, said the partnership with Claro will boost opportunities for Chilean industry to digitalize, expanding the possibility of automation in mining as well as other industrial sectors.
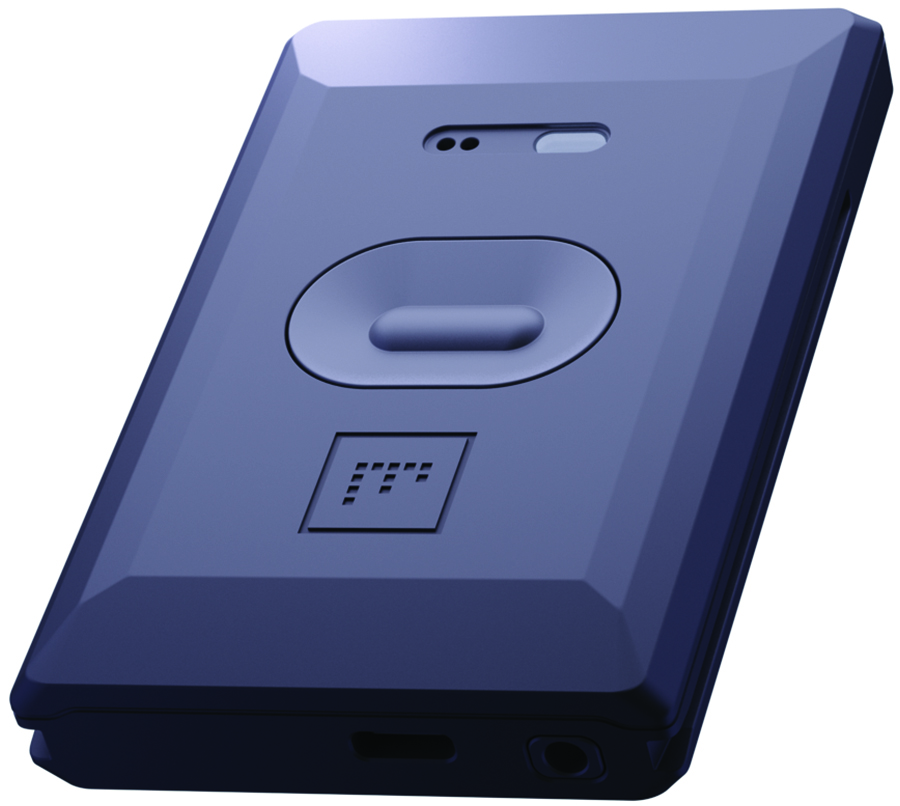
The Mobilaris Companion is a wearable device that provides secure asset tracking, collecting and sending information and positioning data through IoT and cellular technologies.
Major Miners Seek Solutions for Hauler Electrification
BHP, Rio Tinto and Vale recently launched the Charge On Innovation Challenge, a global competition for technology innovators to develop new concepts for large-scale haul truck electrification systems to help significantly cut emissions from surface mine operations and unlock safety, productivity, and operational improvements.
BHP, Rio Tinto, and Vale are the founding patrons of the challenge — which was announced in May — in partnership with Australia’s Mining Equipment, Technology and Services (METS) industry body Austmine. The challenge, according to the founders, is expected to attract additional interest from resource companies that maintain substantial haul truck fleets and are looking for innovative concepts to deliver electricity to large battery-electric haul trucks.
Current stationary charging systems require substantial time to charge large trucks, which would result in significant lost productivity. The mining industry needs multi-megawatt scale fast-charging concepts capable of delivering around 400 kWh to charge (and propel) a truck within the haul cycle.
“METS and mining companies are united on the challenge to reduce emissions across the supply chain,” Austmine CEO Christine Gibbs Stewart said. “We expect the challenge will attract companies from a broad range of sectors including mining, automotive, aerospace, agriculture, and defense to deliver selected charging concepts to create a standard product that can interface with all trucks.”
President of BHP Minerals Australia Edgar Basto said, “We expect the challenge will stimulate innovative ideas, some of which could be immediately applied to existing diesel-electric equipment and help fast-track implementation of longer-term solutions. We understand that these challenges will not be solved overnight, but together we can find the best concepts that can be applied across the industry.”
Carlos Mello, ferrous engineering director at Vale, said, “Mine electrification requires considerable integration between mine planning and operations. We need to develop new charging solutions that can be incorporated into our operations in parallel to the development of battery trucks, to ensure we create a truly sustainable electric haulage system in all aspects – clean, competitive and flexible.”
Several non-traditional mining sector vendors are actively developing technologies that can be applied to mine electrification. The challenge is expected to demonstrate an emerging market for charging solutions in mining, accelerate commercialization of solutions, and integrate innovations from other industries into the mining sector.
The expression of interest process for the challenge began in mid-May, and candidates who make the short list are expected to pitch their concepts later during this year.