Joest successfully completes a project that enables LKAB’s pellet handling and loading operation at Narvik to handle up to 15,000 t/h
Kiruna, the northernmost city in Sweden, is home to the underground iron ore mine of the same name, operated by the state-owned company Luossavaara-Kiirunavaara AB (LKAB). Ore from the Kiruna mine is transported to the port city of Narvik, Norway, over a railway built more than a century ago specifically for this purpose—and at the time, was the northernmost rail line in the world. The trains now traveling this route transport around 33 million tons of product per year, pulling up to 68 railcars per train. A special automated unloading station can unload each of these cars in five seconds.
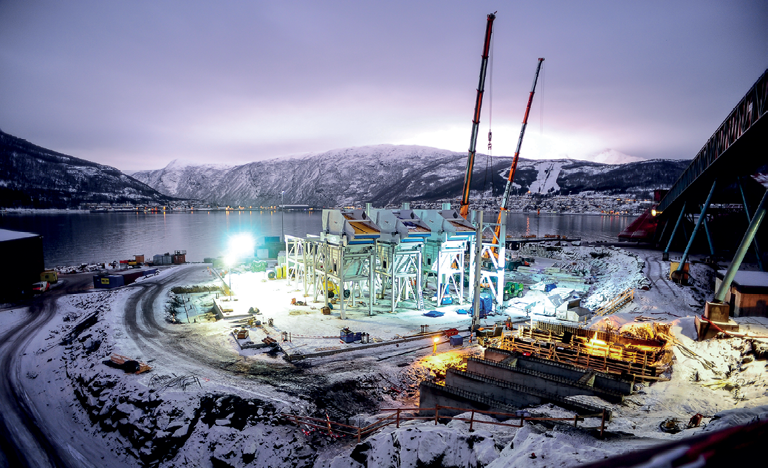
The recently completed, state-of-the-art plant includes six large double-deck vibrating screens and adds 9,000 t/h of capacity to LKAB’s pellet-handling capacity at Narvik.
Narvik is located on the Ofotfjord, north of the Arctic Circle, but the local climate is influenced by the Gulf Stream, providing an average annual temperature of 4°C (38°F). Consequently, the fjord remains free of ice almost all year round, and Narvik is where LKAB carries out direct loading of iron ore pellets onto ships. Recently, LKAB’s existing facility, with a processing rate of 6,000 tons per hour (t/h), was augmented by the addition of a second plant rated at 9,000 t/h. Germany-based vibrating-technology specialist Joest worked closely with LKAB to design the new screening plant, which consists of a storage bunker system, six large double-deck vibrating screens with chutes, various connecting belt conveyors and a crusher. The scope of delivery included detailed planning, project management, installation and startup.
The storage bunker measures 19 x 11 x 13 m and allows LKAB to deliver and store 1,600 m3 of iron ore pellets ranging in size from 11 to 16 mm. Joest designed the system to ensure the bunkers are filled evenly and without loss of product along the way. The steel bunker, which weighs about 350 tons, is split into six equal segments. Each segment is fitted with two hydraulic needle gates. Underneath each of the six bunker segments, a large Joest feeder discharges the material onto a vibrating screen.
Overall, the screening plant measures 41 x 26 x 42 m (135 x 85 x 108 ft), and was constructed using more than 1,700 tons of steel. Each of the six double-deck vibrating screens is 3,000 mm wide and 9,200 mm long (10 x 30 ft). The screens are arranged in a back-to-back position for optimum material distribution. It was very important for the customer to be able to exchange screens separately for maintenance purposes, so two removal positions were set up for this purpose.
Each screen has a maximum capacity of 1,500 t/h and has an effective screening area of 27.6 m2 (33 yd2) per deck. This results in a total screening area of approximately 332 m2—comparable to the size of a lot for a single-family house with a small garden.
The screens classify the input materials into pellets, fines and larger material particles. The pellets are moved directly onto a belt for loading onto ships. The finer material, with a size range of 0–6 mm, reports to a fines hopper for processing into pellets. The larger material, comprising about 2% or less of the feed and ranging from 20–50 mm in size, is conveyed to the oversize material handling facility, where it is reduced by a crusher and returned to the fine material belt conveyor. This allows all of the customer’s material to remain within the process without loss of potential revenue.
The entire plant contains 12 conveyor belts with a total length of 410 m. The belts, ranging in width from 800 to 2,000 mm, move material at up to 3 m/s. All conveyor belts are equipped with a hydraulic tensioning device and longer inclined belts also have a built-in brake to prevent a loaded belt from running backward and discharging its material.
Optionally, incoming material can be sent directly for loading onto a ship via a 23-m bypass belt. The bypass also has the task of handling up to 11,000 t/h of fine ore, which does not need to be screened and can be moved directly to the ship.
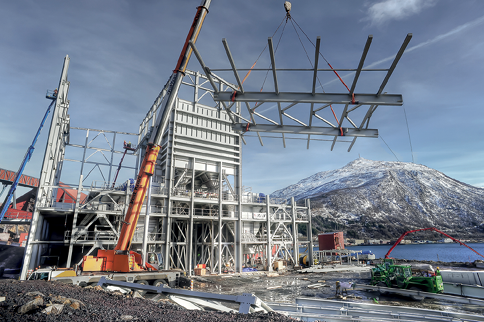
To reduce transmission of vibration, Joest mounted moving components such as screens and hoppers in a steel substructure isolated from the main plant structure.
Among the facility’s notable design elements is the attachment of moving components such as screens and hoppers to a separate steel substructure that is not connected to the screening plant, thereby minimizing transmission of vibration. Screening equipment and bunker discharge feeders are also configured with an isolation frame to reduce the remaining dynamic forces transmitted to the steel structure. This results in an optimized mass ratio between the vibrating equipment and the isolation frame, with an effective degree of isolation exceeding 90%.
The large AC motors driving the screening equipment in the old plant use V-belts, which must be replaced at regular intervals. In order to keep the maintenance costs of the new plant as low as possible, the customer followed Joest’s recommendations to power the new plant’s screens by direct drive, with frequency converters.
After an extensive I/O check to determine, for example, whether all the cabling had been laid correctly and all electrical signals were correct, cold startup took place for each individual machine. To achieve this, each machine was activated and tested separately without load. These successful individual tests formed the basis of cold startup of the entire equipment for automatic operations. Further checks also indicated whether the switch-off intervals between the machines were set correctly.
Warm startup for the entire plant in early April was followed two days later by the first ship arriving at the port, ready to take on cargo from the new facility.
Some of the special challenges involved in this project, according to Joest, included meeting the customer’s high level of requirements, especially in terms of the quality of the equipment, screening efficiency, durability, ease of maintenance and automation. In addition, the outer shell of the screening plant had to be closed-in before the onset of the Scandinavian winter with its cold weather and short daylight periods.
Information for this article was provided by Joest, part of the JÖST Group, which designs and develops system solutions for the processing of bulk materials.
How It All Began
A successful project in 2012 set the stage for Joest’s involvement in the new expansion plant. Four years ago, the company delivered a large double-deck screen with movable hopper discharge feeder to LKAB, successfully designing and installing new, larger equipment in the existing, very narrow screening plant. This convinced the customer that Joest’s technical expertise was equal to the challenge of designing and equipping the new plant, and the company subsequently was selected as the supplier for the project.